Hybrid Propulsion Research
IN Space's research into hybrid propulsion systems began with U.S. Air Force interest in rockets with a high degree of control over their energy release. Controlled energy release in rocket vehicles permits greater mission flexibility and offers the potential to use a common propulsion system for a variety of different missions and vehicles. With funding through the USAF, IN Space has investigated hybrid rocket motor technologies that offer high throttling ratios and multiple restarts to achieve effective energy management.
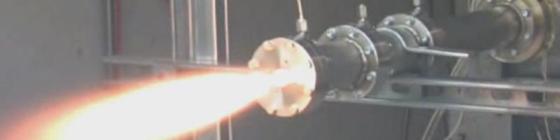
Concept
The hybrid motor concept examined by IN Space used concentrated hydrogen peroxide as the oxidizer and a polyethylene-based grain as the fuel. Hydrogen peroxide was selected for this application given the utility afforded through peroxide’s well-understood catalytic and thermal decomposition mechanisms and the interest in non-toxic propellants. Hydrogen peroxide also has a high density, is storable, and has a higher specific impulse (by 6%) and density-specific impulse (by 19%) than nitrous oxide when used with polyethylene or hydroxyl-terminated polybutadiene (HTPB) fuel grains. IN Space designed, built and tested a 150 lbf thrust workhorse hybrid motor to evaluate the concept for the effective energy management that the USAF is interested in.
Overcoming Typical Hybrid Motor Disadvantages
Unburned or residual propellant in the form of propellant grain slivers is a common problem with multiple port hybrids. This propellant “slivering” often occurs when the grain burns back to the point where the liquid propellant cannot or is impractical to reach the solid remnants. These slivers are thus not used in the propulsion system and become inert weight for the vehicle. By utilizing the decomposition mechanisms of hydrogen peroxide, the hybrid motor investigated by IN Space evenly and efficiently distributes the oxidizer in the combustion thereby minimizing these performance-detracting characteristics of hybrid motors.
Low regression rates are also a typical drawback of hybrid motors, which lead designers to use multiple fuel grain ports to achieve desired thrust levels. This, in turn, leads to propellant slivering and lower volume efficiency of the propulsion system. Test firings of the hybrid motor technologies investigated in this research effort reached regression rates over 0.11 inches per second with advanced fuel grains. These high regression rates permit fewer fuel grain ports – even single ports are possible for upper stage thrust scales – which results in a smaller and lower inert weight propulsion system.
Throttling
Substantial throttling capabilities were demonstrated through testing in relevant mission scenarios. Throttle-down tests (video below; high quality video on the Multimedia page) exhibited a 10:1 throttling ratio with stable combustion across the entire range. Boost/Sustain thrust profiles were also tested with 75%, 50%, and lower sustain-to-boost chamber pressure ratios with rapid throttle-up. Testing also verified that throttling up from the nominal conditions by modest amounts to maintain the optimum mixture ratio was possible. Similarly, the hybrid motor can be throttled to decrease a vehicle’s acceleration and lessen aerodynamic forces or to maintain the optimum mixture ratio for maximum delivered impulse efficiency.
Multiple Start
The use of an energetic monopropellant as the oxidizer in the hybrid motor affords several paths to achieving effective ignition of the fuel without a separate, consumable ignition system. This passive ignition feature allows the propulsion system to be restarted or pulsed any number of times so long as propellant remains. Relight of a rocket motor can be useful for a variety of mission scenarios that may benefit from utilizing the same stage following a coast phase including a circularization burn with an upper stage for Low Earth Orbit insertion, lunar orbit insertion using the Earth departure stage, or using a launch stage for a pulsed or throttled operation to achieve a soft landing. Further, multiple start capability is a significant safety advantage for human-rated launch vehicles and a requirement for steering and attitude control systems during launch, on orbit, or in rendezvous.
The hybrid motor concept investigated by IN Space on the 150 lbf thrust scale explored two different ignition approaches in dozens of test firings. Chamber pressure data of optimized conditions showed reliable, repeatable ignition events followed by stable combustion indicating utility of the hybrid motor in relight scenarios.
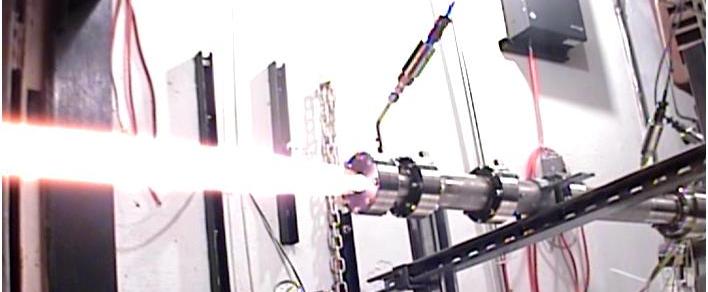